"The Maple Leaf Photonics system is at the center of our iterative design process, since commission it has been in use continually."
Dr. Cedrik Coia, team lead test development and prototyping at AEPONYX
Dr. Cedrik Coia has years of experience with fabrication processes for Micro-Electro-Mechanical Systems (MEMS) devices. He is the test development team lead at the Canadian startup AEPONYX, a fabless micro-optical switch semiconductor chip designer and manufacturer. AEPONYX combines MEMS and silicon nitride-based photonics to design demultiplexer filters. With decreased power consumption and up to 100x increase in speed, AEPONYX's waveguide devices are seeking to revolutionize optical communications, especially in data center applications. Using the Maple Leaf Photonics system, AEPONYX is able to keep their testing needs up to speed with their fabrication quantities.
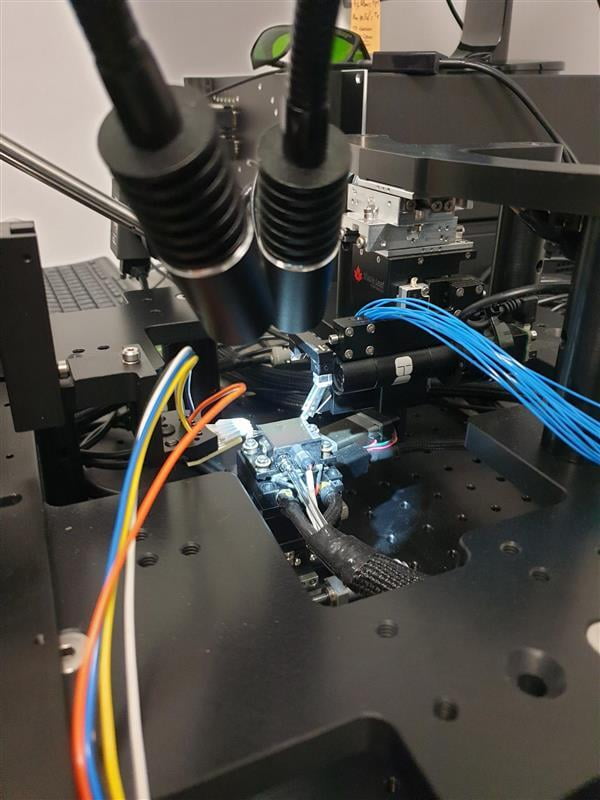
Optimizing the Design Process from Fab to Lab with an MLP System
The design and fabrication of demultiplexer filters at AEPONYX required advanced testing methods that couldn't be done manually. Prior to purchasing their own Maple Leaf Photonics system, AEPONYX had been using their partner university's MLP photonic probe systems. As their fabrication runs grew larger and more frequent, they realized the throughput and turnaround time for testing was the greatest bottleneck in their iterative design process. With previous exposure to the MLP system and evolving testing needs, AEPONYX decided to purchase their own MLP probe system.
Maple Leaf Photonics provided AEPONYX with a system optimized for testing the demultiplexer filters given the stage of development they were in. After installing their own system, AEPONYX was able to focus on the data analysis. To handle the amount of data they were receiving from the continual operation and automated testing of several hundred devices on the chip, AEPONYX quickly automated their data analysis. “The throughput and the turnaround time MLP provides by having quick access to data really speeds up the learning process of the team--both the designer part of the team and the tester part of the team,” Dr. Coia affirmed.
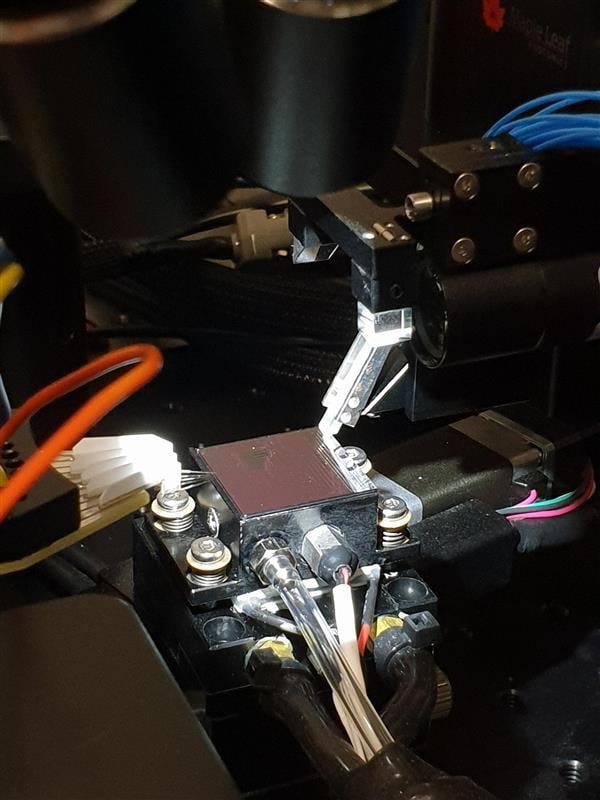
With the increased throughput, repeatability, and reliability, AEPONYX has been able to understand the bias between design and the fab that you can't see in simulations. Being able to account for this in designs has sped up their ability to fine tune their designs and reach production level faster.
Dr. Coia expressed that the transition to using their own MLP system exceeded their expectations in many ways, but “the best asset we had from MLP was their collaboration. The technological knowledge that they come up with, they have been very supportive all along in the process, and that was key to get the setup to where it is.” Dr. Coia added that "as a startup, we appreciated the relatively low cost and the hands-on support from Maple Leaf Photonics to help us automate our testing."
MLP Brings New Levels of Productivity and Understanding to the Design Process
Dr. Coia also reports that the MLP setup has been crucial in the development of the demultiplexer filter and is "at the center of our iterative design process. It’s being used almost on a 24-hour basis. Every day there is a sample running on the MLP setup.” Built-in functionality for efficiently and reliably finding first light proved to be at the center of the MLP system’s ability to automatically measure many devices in succession without human intervention. This produced much more comprehensive data sets that invited development of innovative automated data analysis tools for processing and interpretation. “We've been able to sample comprehensive DOEs with hundreds of instances on each chip to be able to match our design with the fab," explained Dr. Coia, "to that regard the MLP setup is a work horse." The impact is a robust statistical process control environment for design optimization and foundry quality management.
Summarizing the AEPONYX experience with Maple Leaf Photonics, Dr. Coia said he “couldn’t imagine doing this kind of assessment without having a semi-automated tool like the MLP setup.”
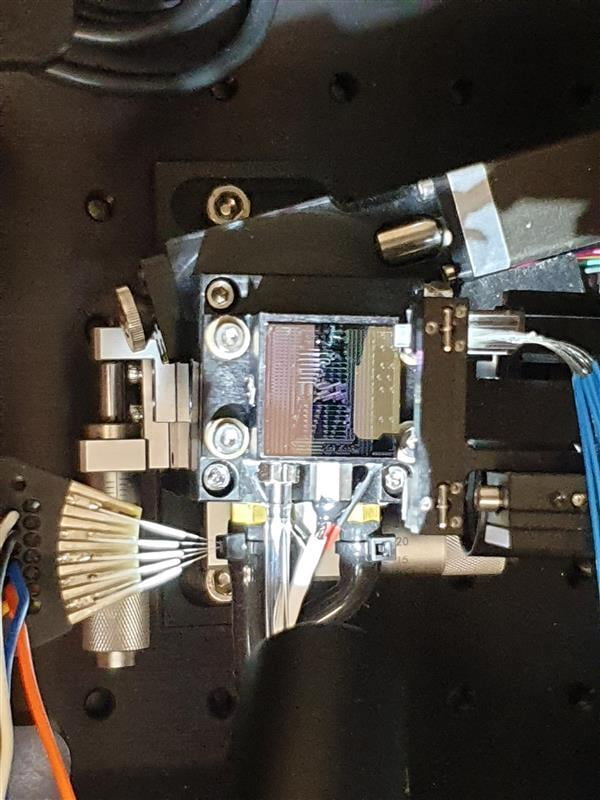